Today we visited Codelco’s Chuquicamata mine, the largest open-pit operation in the world. 460,000 tonnes per day of material is moved with 160,000 of that being ore sent to the mill.
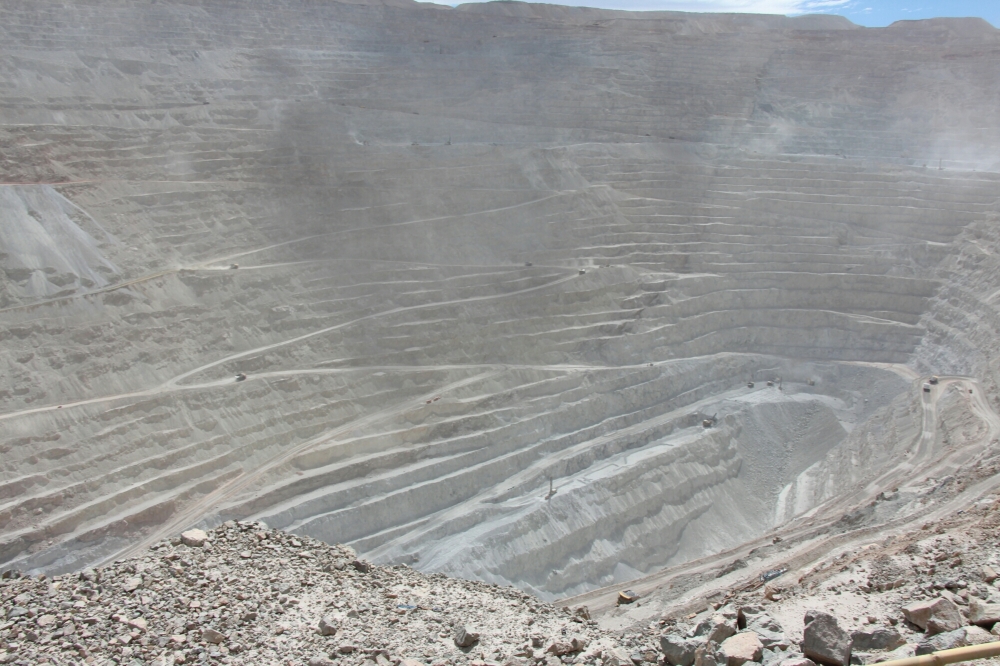
The day began with Codelco graciously providing us with transport from our hotel in Calama to the mine site. As we boarded the coach bus all personal protective equipment was provided, again highlighting Codelco’s regard for safety as witnessed at Andina.
The first part of our tour consisted of visiting the mine’s processing plant. Accompanied by the Mill Superintendent, we viewed the sites dewatering facilities, considered to be one of the best in the world in terms of water reuse. Chuquicamata draws water from 4 naturally occurring springs on site as well as transporting water from the Andes Codillera. The milling process uses 2 cubic meters of water per tonne of ore milled, with 75% (1.5 cubic meters) being recycled. Being situated in an arid climate, this is one of many factors that allows for Chuquicamata to remain competitive with other operations. The picture below shows one of the nine 350-ft diameter thickeners that are utilized on site.

After this, we visited the chuquicamata copper concentrator. The operation has a combined throughput of 160,000 tpd. Initially the mill was constructed for a 40,000 tpd operation during the early life of the mine. However, as the copper markets evolved and the deposit further explored, an extension of the mine life as well as an increase in throughout became feasible. As a result, a secondary plant was constructed to accommodate the additional tonnage.

The mineralization at Chuquicamata is primarily sulfide copper. Sulphide ore is processed in the concentrator. The mill feed is supplemented with sulphide ore conveyed from Coldelco’s nearby Radomiro Tomic mine. Radomiro Tomic is primarily a heap leaching operation which processes oxide copper material. As a cost saving measure, Radomiro Tomic does not have its own sulphide processing plant but instead conveys sulphides to Chuquicamata.

The mill employs two 32-ft SAG mills feeding a complex arrangement of rod and ball mills. A final grind size of 219 microns is achieved before the slurry is passed on to flotation.
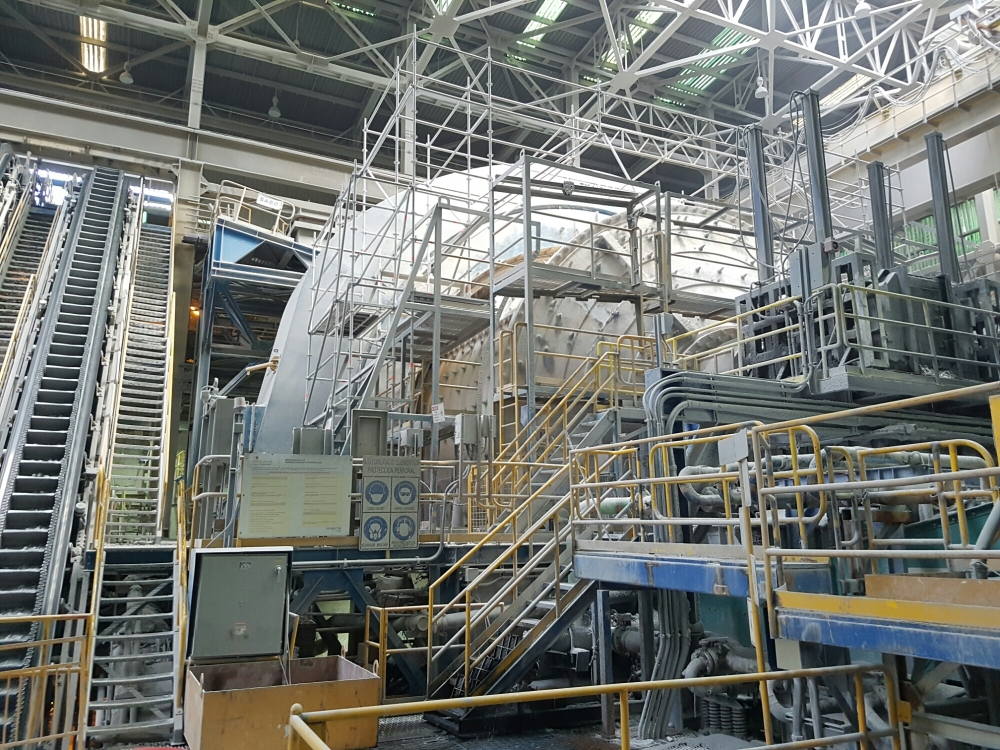

The mill head grade for sulfide processing is approximately 0.8% Cu and also contains significant amounts of molybdenum making two separate concentrates viable. The final copper concentrate is smelted and then refined prior to shipment, both processes are carried out on-site and were part of the next stop of our tour.
The concentrator contains a separate circuit for recovery of copper from the on-site smelter slag. Slag can contain between 8 and 10% Cu and is sent to its own process line containing a SAG mill two ball mills, and floatation circuit.

Codelco operates three refineries to produce its final copper product from its smelting processes. The refinery at Chuquicamata refines product from not only its own operations, but as well as the El Teniente and Altonorte smelters to ensure it remains at capacity.
Fortunately during our tour, scheduled maintenance was being carried out in many areas of the refinery allowing for us to get an unprecedented up-close look at the plant.

The refinery upgrades anodes produced from smelting to 99.9% Cu from 99.6%. Each anode is placed in tanks and copper is deposited on both sides of a steel cathode as electrolysis is carried out over an 18 day residence time to produce the final copper product. As an interesting note, our tour guide mentioned that Canadian made machinery is used in the process to split the copper sheets from the steel cathodes. The byproducts from refining is collected to produce a gold, lead and antimony bar for sale. According to the numbers provided during our tour, this refinery produces approximately 2.5 million lbs of copper each year!
The image below shows a copper anode (the product of the smelter) before refining (99.6% Cu).

The image below shows a copper cathode (the product of the refinery) which grades at 99.9% Cu.

To finish off the tour before departing, we viewed the open-pit from a lookout point where we could grasp the scale of this giant mine. A fleet of 82 haul trucks passed us by as we took photos and thanked our tour guides for their hospitality, without it this amazing tour would not have been possible.

– Maher Chaudhary